Aluminum electrolysis it is the most energy-intensive process that uses direct current Potline DC current could be up to 500 kA and 1500 V DC. With such load parameters parallel connection of rectifier groups is used. ‘N-1’ principle is implemented – with switch-off of one rectifier group, the total potline current is not reduced. Usually are installed diode rectifiers, transformers with OLTC and saturable reactors. Применяются диодные агрегаты с дросселями насыщения ДН. The DC supply reliability requirements are the highest, as any significant interruptions in power supply (more than 5 … 10 hours), lead to irreversible damage of the main technological equipment – electrolysis pots
Our specialists have been involved in almost all projects implemented at Russian aluminum smelters since 1995. These are Kamensk-Uralsky, Volgograd, Novokuznetsk, Bratsk, Krasnoyarsk, Irkutsk, Sayanogorsk, Boguchany and Taishet aluminum smelters, all now UC RUSAL, the Aluminum Company of Egypt. The first rectifier unit with microprocessor control was developed with the participation of our specialists in 1997.
At the moment in the world two main aluminum smelting technologies are present: Soderberg (DC current up to 180kA, DC voltage up to 1000V) and pre-backed anode (DC current up to 500kA, DC voltage up to 1570V). Rectifier groups could be of two main design:
- With separate rectifiers, installed in capital building (rectifier group current 25kA or 32kA, often of old Soviet design). Separate design of cooling system.
- With integrated rectifiers of high factory readiness. Each rectifier is installed, together with its cooling and control system, in a separate shelter. One-unit current is up to 100 kA. No special building is needed.
For the 25/32kA unit, LLC “ETS Engineering” has developed and is supplying rectifiers with air forced cooling system, as well as units with liquid cooling system (depending on a particular smelter), cooling system, microprocessor control cabinets for a single unit and the current control system of the whole potline. Oil-immersed transformers could be in delivery scope.
Rectifiers of shelter design supplied factory assembled and tested.
Rectifiers from ETS Engineering have the following features:
- operation 24/7;
- rectifier group layout modification to suit existing space and AC/DC busbar system if exists;
- current (voltage) regulation by transformer OLTC and smooth regulation by saturable reactors;
- “n-1” operation mode – rectifier provides rated DC current without one semiconductor in leg;
- every semiconductor is protected by a high-speed fuse with blow indicator, giving a signal to control system;
- special design, which ensures the alignment of currents along parallel branches;
- non-flammable insulation materials;
- advanced rectifier diagnostic system;
- easy integration with enterprise control system.
Boosting rectifiers (25 … 70 kA) are designed for local current increase in individual sections of potline (for example, experimental sections with high-current pots). They are made in shelter design for outdoor placement, with high factory readiness and are equipped with oil conversion transformers.
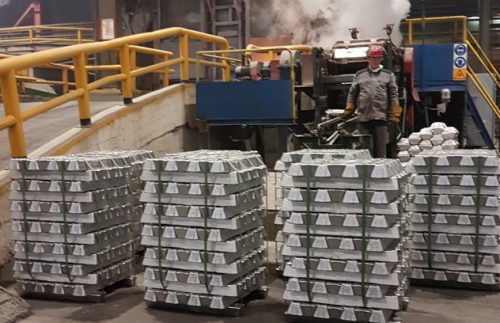
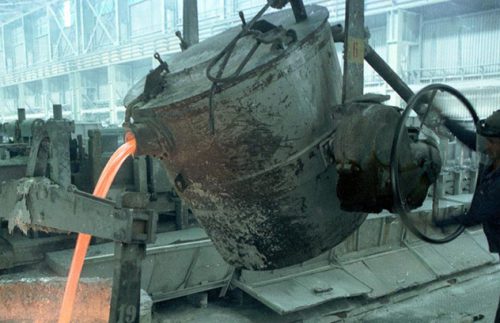
Full set of factory tests of all equipment and software significantly reduces the cost of putting equipment into operation. All documentation provided includes comprehensive instructions for operational and maintenance personnel, including electrical diagrams of all components.